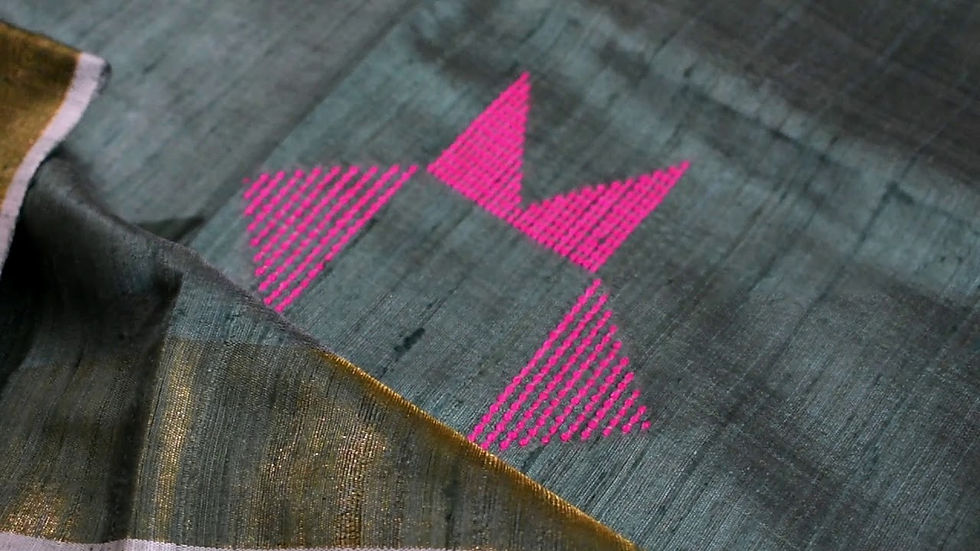
The crisp, paper-like Kosa silk is popular not only in India but abroad too. Besides sarees and salwar suits, the fabric is used to create lehengas, stoles, shawls and menswear including jackets, shirts, achkans and sherwanis. The sturdy kosa yarn is obtained from cocoons after the fully formed silkworm moths leave them.
Indigenous to Champa, Bilaspur, Raigarh, Jagdalpur and Bastar areas of Chhattisgarh, where the weaving is done by the Devangan community, the silk is valued for its texture which lends itself beautifully to printing and painting and is therefore increasingly used in designer boutiques to craft some of the most innovative motifs ever. It would be no exaggeration to say that the fabric is an ode to the imagination of the weavers, as each of the typical Fera and Jaala weave patterns seems to narrate its own special tale, with inspiration drawn from sources ranging from Nature to mythological stories.
Kosa silk is drawn from cocoons grown specially on Arjun, Saja or Sal trees and are obtained naturally in shades of cream, honey, beige, yellow and ash. However, these natural hues are tastefully dyed using dyes made from vegetables, fruits, flowers, pollen, lac and other natural substances. The Kosa cloth is available in a range of colours and patterns that are block-printed, painted or embroidered.
Particularly famous are the kantha-embroidered Kosa wear which chiefly involve floral and abstract designs made of small running stitches in a medley of colours ranging from the riotous to the more sober pastel shades.
Each cocoon woven by the kosa silkworm yields 1-2 grams of raw silk yarn, equivalent to about 300 yards of thread. However, due to the rarity of the kosa worm and the laborious cost of cultivating it, the raw silk yarn is often used to create blended yarn with cotton or polyster. The price of a kosa sari may range from as little as Rs. 400 to several thousands, depending on the purity of the silk as well as the handwork and accessories used on it.

Weavers typically design simple sarees Gamchha and Mailoonga worn by the Kanwar, Gond and Baiga tribals of Chhattisgarh. Then there are the special dresses woven out of coloured threads for the folk dancers of the region who perform the Tual and Dhruva Bandhipata dances. At the top of the list are bridal and party-wear sarees exquisitely woven with gold and silver thread-work on them. A simple kosa saree may take about three to five days to produce from yarn extraction to the weaving depending on the number of people working on it, says Chandramani Devangan, proprietor of Kosa Kala, a retail outlet in Chhuri village of Champa district, where over 200 weavers seek their livelihood from the art. Each village turns out patterns unique to it.
The sturdy kosa yarn is obtained from cocoons after the fully-formed silkworm moths leave them. Called Gichha, this coarse yarn is higher priced than the fine silk yarn as it is more durable, says Devangan. During the extraction of yarn, there is often wastage in the form of cut threads. These bits are used to craft accessories such as trendy purses, handbags and even jewellery pieces.
The story of kosa silk however does not end with fashion accessories and clothes! A range of chic utility items and décor objects are aesthetically produced from a third type of yarn that gets woven on tree twigs by the kosa larvae. Produced naturally in only two colours black and cream this sturdiest form of yarn is used to make doormats, rugs and cushion covers, often adorned with mirror and embroidery work.
Kosa's growing popularity in urban centres is in turn giving hundreds of village women a new lease of life. For, the yarn extraction is done entirely by women and the men only weave the fabric. The women's income is helping their children, especially daughters, gain education at the village schools. Even as they are keen to keep the weaving tradition alive and gain a wider market for their products, the community appears unwilling to pass on this means of livelihood to its children. Instead they prefer the next generation to look for white-collar jobs in the bigger towns and cities.
コメント