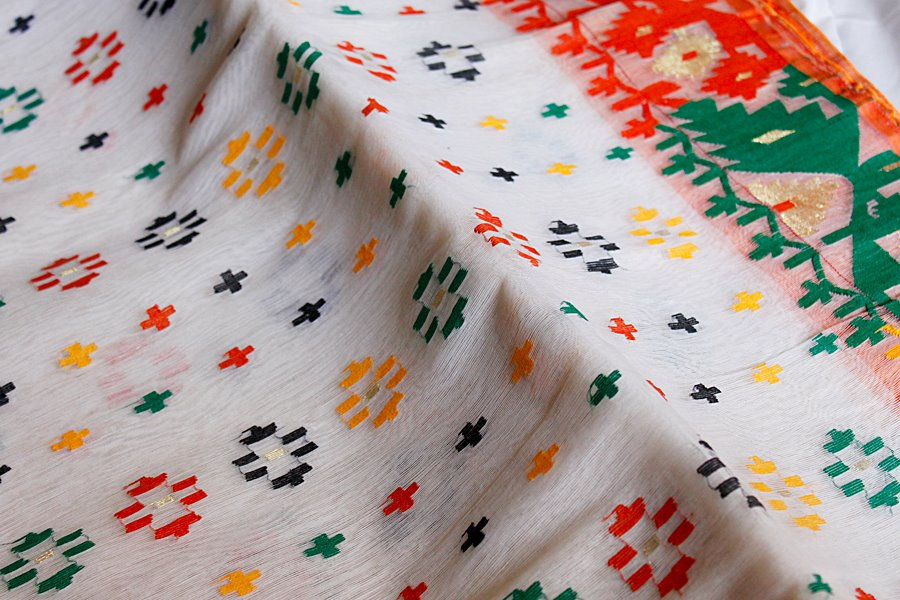
One day, the Mughal emperor Auwrangzeb was astonished to see his eldest and favorite daughter, Princess Zeb-Un-Nissa, strolling naked in the garden. Outraged by her immodesty, the emperor demanded to know why she was walking outside without clothes. The princess calmly replied that she was wearing her “jamas”. In fact, she claimed she was wearing seven garments sewn from a jamdani so transparent and fine that to her father’s eyes they seemed invisible.
This 17th century story is one of the earliest known references to jamdani, a fine, hand woven figured muslin produced in Bengal. Thicker cotton threads are laid into the weft to produce the illusion of a suspended pattern on the surface of an almost transparent fabric. Intricate colored motifs seem to float upon the cloth. The word jamdani is thought to have derived from jaam-daar, a Persian weaving term for floral designs in cotton thread or possibly, jama, the Bengali word for dress.
Production of jamdani reached a pinnacle during the latter period of the Mughal empire. The ultimate test of its fineness was to pass a sari width through a small golden ring. Centuries before the arrival of the Mughals, the Bengali textile industry had exported fine cotton muslins to both Roman and Chinese empires. The Greek geographer Megasthenes described Bengali muslins in the 4th Century BC. The Romans were so inspired by the fabric’s diaphanous quality they called it “woven air”. In the 17th and 18th centuries, the fabric became a much desired and expensive trade good exported west to Kabul, Baluchistan, Persia, Arabia and Greece. Jamdani continued to be produced and exported during the days of the British Raj, but the British supported their own agriculture and textile industries at India’s expense, and the quality of Bengali jamdani declined. Recently, quality has returned with revived interest in traditional Indian textiles. Today, jamdani is produced more or less as it has been for centuries.
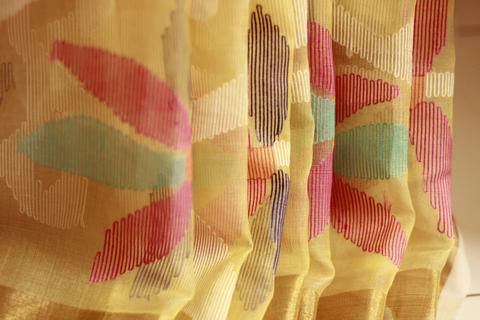
Making jamdani is very labor-intensive requiring specialization that is divided amongst workers by religion, village and, especially, gender. The work generally involves a community of artisans, often a family of weavers or dyers cooperating in accordance with years of tradition like a carefully calibrated clock. Work is scheduled according to the season of the year and the time of the day, choosing the most appropriate moments for the practice of various tasks. Most of the weavers are Muslims who believe figurative representations in art are a direct challenge to the omnipotence of God. For this reason, artisans create motifs drawn from nature or abstract designs with a geometric sensibility. Pit looms are still used, however, the original throw shuttle has been replaced by the fly shuttle, a faster and more efficient method of production that still depends upon the hand for guidance. Traditionally, the plain weave background was white, off-white or grey; today background colors are chosen from a vibrant array.
The best quality jamdani is produced with locally grown, fine cotton. It is always woven during the monsoon season from June to October when the air is humid and moisture prevents the fine threads from becoming brittle and breaking. Bundles of thread are dyed in a variety of colors. The dyed thread is strengthened and softened by soaking overnight in a solution of rice water starch, allowing the women to wind it more easily onto bobbins. It is tedious work done early in the morning, usually between 4 and 9, before the increasing heat dries the thread, making it more difficult to handle. The wound bobbins are sent to another worker who prepares the warp on a beam. Afterwards, the warp is sent to the weaver’s house where it is set up on a loom. Drawings are placed under the warp as a guide. The weaver, almost always a man, may or may not follow the drawing, often preferring to work from intuition alone. Colored thread is carefully inserted and hand tied into the fine weft to create patterns on the plain weave.
The entire system of production, from dyeing the thread to setting up the loom, is determined by the length of jamdani’s most marketable end product, the sari. For this reason, it is nearly impossible to convince weavers to produce different lengths of running yardage. Looms are set up with 11 meter warps, each warp yielding two saris, 5.5 meters in length. The patterns woven into these two saris will not be repeated by the weaver again.